Jonathan Prestwich
Jonathan Prestwich
MF: How did you first get involved with Modus?
JP: I had moved back to London from France where I was living and working as an employed designer then I joined the design studio of Barber Osgerby for a short period. I had a couple of good leads for some projects so I thought, very naively, that I’d give it a go and start up on my own. I started trawling the design fairs and that was when I met Ed from Modus. I just started to talk to him and we got on really well and he invited me to show him some of my project ideas. They were really ‘blue sky’ projects; things that had never been done before but had the possibility to be easier to assemble, easier to produce and with greater comfort than anything before in its price range. The interest was there so we started our relationship like that. The first project we completed was called the OS chair, which was pretty much one of the first chairs that I had produced under my own name as a self-employed person.
MF: And since that first product, how has that relationship with Modus evolved?
JP: We have a good working relationship and we’re always trying new things. As well as doing the blue sky pieces, we aim to create some solid furniture that performs well in the market. With Modus, we’ve always tried to have a point of difference and something that’s a little bit better than everyone else’s – or more relevant.
MF: How do you justify adding more to a market that’s already pretty full?
JP: It’s very challenging but there’s now a greater need for innovation and to have something that’s more culturally relevant. When I talk about culture, I’m exploring opportunities within the office culture or that of a canteen space, for example. It’s fascinating to study the ever-evolving ways of working and these new environments are ripe with opportunities.
Contrary to this, a negative side to the market is the constant desire for newness, which means that products don’t necessarily last as long and clients seem to expect more regular launches and quicker releases.
MF: What shifts have you noticed with office culture?
JP: It’s fantastic that employers are now thinking about the wellbeing of their staff within the workplace, which wasn’t talked about much 20 years ago when there was more emphasis on an office’s outward appearance to clients. Wellness and improving productivity is something that we focus on a lot, whether it’s giving people the opportunity to move away from the desk and to work in a more comfortable environment or create more appropriate spaces for small meetings as well as larger ones. We do it in a way that helps people feel relaxed as they would at home.
Modus has always produced furniture that can fit into multiple environments. Maybe intuitively they knew that the domestication of the workplace was coming.
MF: What process do you go through to develop a new product?
JP: I would start with some sketches and propose a general direction with a few options. At that stage, I’m considering the presence of the product - is it going to be more corporate, is it going to be more domestic, is it going to be strong, is it going to be sturdy, is it going to be light, is it going to be elegant etc. Those are the first kind of things that we’re looking at, striving to create the mood that the people around that object can pick up on. It’s kind of like starting at the end, imagining how the users will behave with the product.
Once that part is agreed upon, then we come back to the beginning and question, what the object needs to be to create that final output. So we go to the end first, try to visualise it and then come back to the beginning and work through it. We work in a very hands-on way with physical models but we also work with computer-aided design and we’re always trying to move in and out of the digital world. It’s rather like a sculpture: we start with the very basic object in its most crude form and then we continually refine the structure and the surfaces.
MF: Is there a criteria that applies to the designs that you introduce?
JP: When you’re developing a design, it’s like the difference between a good dancer and a bad dancer (even though I’m more of a bad dancer!). A good dancer creates some beautiful forms with their body, with a great posture and that’s what you want from the product, that it has a good posture, that it holds itself well and that it has an understandable structure. If a chair doesn’t have a clear structure you’re going to question if it’s alright to sit on. It’s not going to give you confidence.
Designing isn’t just about creating a structure that works, it’s also important for that structure to communicate to the user. I’m always trying to understand how and why people make their selections and I believe that comes down to a familiarity and a natural understanding that people have over a product. If you get it wrong, people instantly know and will not buy that furniture. If you get it right, it will sell like crazy. So it’s about balancing the motivation to create something new, beautiful and more relevant with the need to imbue the design with some familiarity. That’s pretty tricky.
MF: Are there any innovations you're particularly excited about right now?
JP: One of the things is 3D printing. Although it’s been in existence for years and years, it’s becoming more and more sophisticated. As designers, it’s allowing us to venture away from the constraints of typical tooling and typical production techniques.
Everyone always asks, “how can you design another chair?” but all of a sudden there’s a whole new media to create any amount of new designs that you want. What we can do with that is create more efficient, more organic and more adaptive furniture.
MF: And where do you see that technology in a decade from now?
JP: Maybe you’ll be able to print a chair and throw it into your own recycler and print another one the next day in your own home. Maybe you only paid five pounds for the file to have that chair produced and you use it for a week and you buy another five pound file from another designer and then you recycle that material. Maybe (and hopefully) it can be done in a way that is not damaging to the environment.
MF: A chair a day – there’s a thought! And where does that leave the designer?
JP: It’s like digital photography, everyone can take and print their own pictures but photographers still have a role in this world. So the designer’s role will hopefully be secure.
Words - Max Fraser
Photography - Mark Whitfield
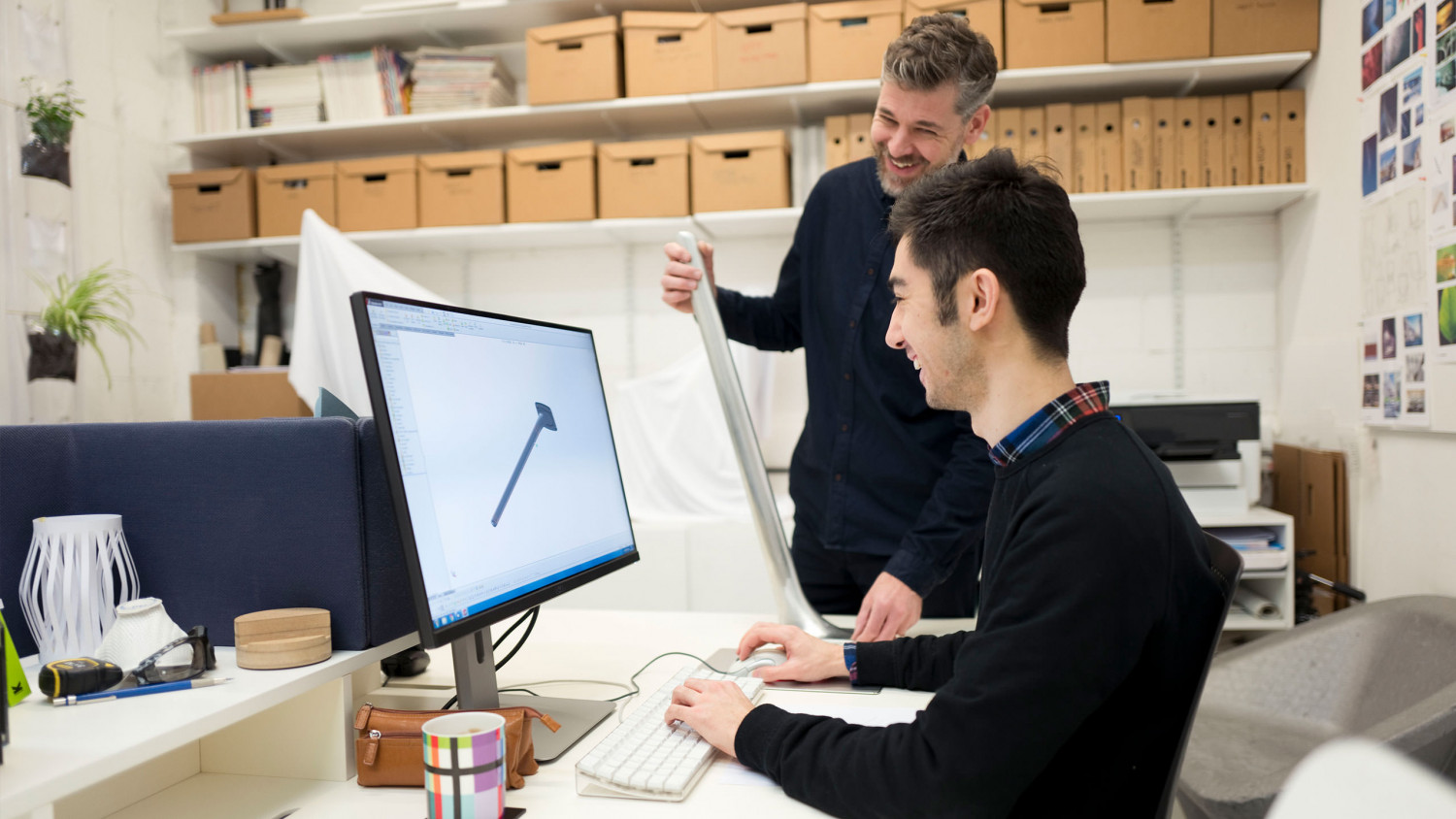
Jonathan Prestwich
Jonathan Prestwich
Jonathan Prestwich
Jonathan Prestwich
Jonathan Prestwich
Jonathan Prestwich
Jonathan Prestwich
Jonathan Prestwich
Jonathan Prestwich